Wondering if someone can tell me where I’m going wrong.
I have a virtual Apex Outlet that triggers an automation on Home Assistant, I have the outlet set to Auto in ApexFusion and seem to have the trigger working when ATO_LO is OPEN, it starts my HA automation which is attached below
What I’m trying to do, is when the ATO is low then turn on the RO system with a pre-flush and run for a max of 20min and a post-membrane flush, then shut off.
What is happening is, the automation is triggered, then a few seconds later my Apex switches the outlet OFF, not remaining on Auto then moving to the Auto-OFF, just off.
I can’t see what I might be doing wrong here, I would assume that it wouldn’t be the apex coding that is turning the outlet completely off, but not sure if my HA automation is causing it.
Original:
Fallback OFF
Set OFF
If ATO_LO OPEN Then ON
If ATO_HI CLOSED Then OFF
When On > 025:00 Then OFF
Defer 000:30 Then ON
Defer 000:30 Then OFF
Updated:
Fallback OFF
If ATO_LO OPEN Then ON
If ATO_HI CLOSED Then OFF
When On > 025:00 Then OFF
Defer 000:30 Then ON
Defer 000:30 Then OFF

I have a virtual Apex Outlet that triggers an automation on Home Assistant, I have the outlet set to Auto in ApexFusion and seem to have the trigger working when ATO_LO is OPEN, it starts my HA automation which is attached below
What I’m trying to do, is when the ATO is low then turn on the RO system with a pre-flush and run for a max of 20min and a post-membrane flush, then shut off.
What is happening is, the automation is triggered, then a few seconds later my Apex switches the outlet OFF, not remaining on Auto then moving to the Auto-OFF, just off.
I can’t see what I might be doing wrong here, I would assume that it wouldn’t be the apex coding that is turning the outlet completely off, but not sure if my HA automation is causing it.
Original:
Fallback OFF
Set OFF
If ATO_LO OPEN Then ON
If ATO_HI CLOSED Then OFF
When On > 025:00 Then OFF
Defer 000:30 Then ON
Defer 000:30 Then OFF
Updated:
Fallback OFF
If ATO_LO OPEN Then ON
If ATO_HI CLOSED Then OFF
When On > 025:00 Then OFF
Defer 000:30 Then ON
Defer 000:30 Then OFF
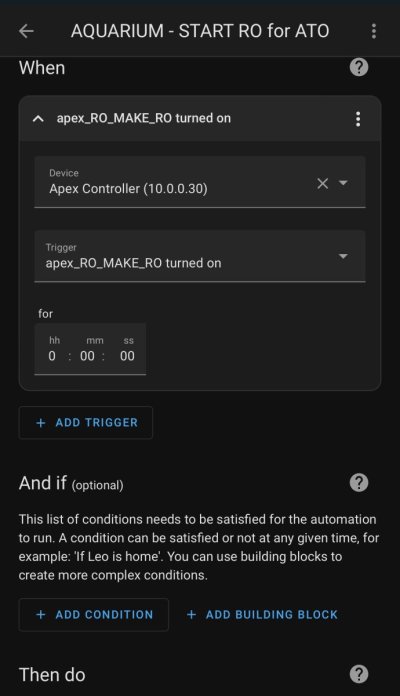
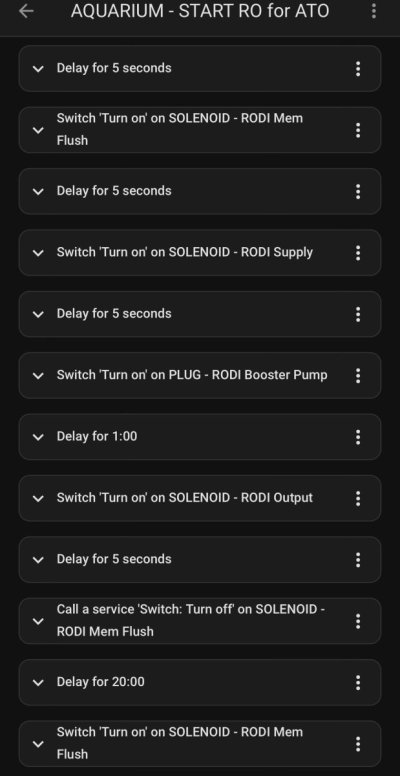
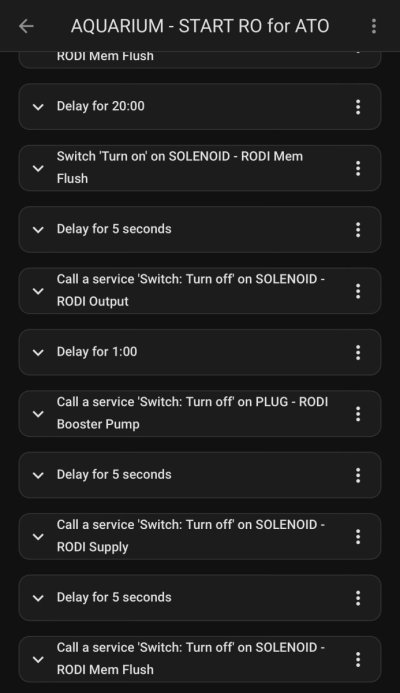
